With the vigorous development of China’s economy and changes in the international situation, the world is paying more and more attention to environmental issues. To respond to the national policy, our company formally set up an environmental protection research group in 2018, and after analyzing the feasibility of all kinds of environmental protection facilities and measures, we decided to use water based ink printing to replace traditional solvent printing.
Characteristics of Water Based Ink Printing
In terms of environmental security, water based ink printing has advantages that traditional solvent-based printing can not be compared. Specifically as follows:
Food Safety Aspects
Through the reform of the color material, and the use of a water and alcohol mixture instead of the traditional solvent-based ink in the volatile solvents, thereby reducing the solvent residues contained in the finished product, there is a forward-looking improvement in food safety.
Peak No. | Compound Name | Retention Time (min) | Peak Height | Peak Area | Content (g) |
---|
1 | Isopropanol | 5.807 | 43.393 | 219.200 | 0.0280 |
2 | Ethyl Acetate | 7.148 | 1099.318 | 4969.800 | 1.2618 |
3 | n-Propanol | 10.457 | 479.298 | 2772.950 | 0.7401 |
4 | Butanol | 17.748 | 322.333 | 2936.650 | 1.2061 |
Total | 1944.342 | 10898.600 | 3.2360 |
Peak No. | Compound Name | Retention Time (min) | Peak Height | Peak Area | Content (g) |
---|
1 | Ethanol | 5.473 | 80.552 | 395.850 | 0.0626 |
2 | Ethyl Acetate | 7.165 | 821.849 | 4113.800 | 1.0445 |
3 | n-Propanol | 10.490 | 44.429 | 257.300 | 0.0687 |
Total | 946.829 | 4766.950 | 1.1758 |
- Through several solvent residue tests on different finished products, the solvent residue of water-based ink finished products is about 36% of solvent-based ink finished products (which contains volatiles produced in solvent compounding, the next step will be to improve the composite raw materials, completely using solvent-free composite instead).
Environmental protection
China’s latest release for the key industries’ volatile organic composite remediation program, the requirements of the printing industry, the total VOCs volatile concentration of less than 80mg / m3 can be discharged, the concentration of disorganized emissions shall not be more than 5mg / m3. Failure to comply with the provisions of the enterprise to suspend production fines and rectification, the maximum penalty for the revocation of licenses and penalties.
Our company invites the third party testing organization to test the ink workshop, and the test result is that the volatile concentration of VOCs is only 28.8mg/m3. It is far less than the national VOCs volatile concentration, which is in line with the emission without treatment. The traditional solvent-based ink process must be paired with end-of-pipe treatment equipment, and the concentration after treatment is close to 110mg/m3. This proves that the water ink process is in full compliance with the national policy in terms of energy saving* and environmental protection, and can add to the national environmental protection cause.
Toluene | Average Emission Concentration | ND | — | mg/m3 |
Average Emission Rate | <3.7×10-5 | — | kg/h | |
Xylene | Average Emission Concentration | 0.02 | — | mg/m3 |
Average Emission Rate | 7.5×10-5 | 1 | kg/h | |
Total VOCs | Average Emission Concentration | 28.8 | 120 | mg/m3 |
Average Emission Rate | 0.11 | 5.1 | kg/h | |
Toluene and Xylene Combined | Average Emission Concentration | <0.03 | 15 | mg/m3 |
Average Emission Rate | <1.1×10-4 | 1.6 | kg/h |
Notes:
- “ND” indicates that the measured result is below the detection limit of the method.
- “–” indicates not applicable or not required.
- The reference standard is the “Printing Industry Volatile Organic Compound Emission Limits” (DB44/815-2010) Table 2 Simple VOCs Emission Limits for “flexographic printing, gravure printing, screen printing, and flatbed printing.” Phase II values provided by the client.
- If there are inconsistencies with the referenced standard, please refer to local supervisory authority guidelines.
※ The concentration of solvent-based process before treatment is about 1000mg/m3, the end processing equipment requires a large number of electric heating equipment in operation, while the adsorption material in the equipment is non-degradable hazardous waste, which needs to be replaced by professional organizations on a regular basis.
Comprehensive environmental remediation program for raw materials containing VOCs ≤ 30% can not do the treatment of disorganized emissions, the new regulations in 2021 (trial) this data is adjusted to ≤ 10%. Ink through the SGS authoritative testing, VOCs content of 7.8%, in full compliance with the latest environmental requirements.
Production Technology
The diluent used in the ink process is a mixture of alcohol and filtered water, the ink itself does not contain hazardous chemicals, and the ink itself is non-flammable, which not only realizes the production safety and health of employees but also ensures the safety of finished products.
At the same time, because of the low volatility of the low concentration of alcohol itself, the viscosity of the ink can be guaranteed to be stable during the production process, and the stability of the printing hue is greatly improved.
Sustainable Development
In 2020, our company took the lead in designing and customizing a brand new special machine for water-ink printing together with the machinery factory, redesigning and transforming the traditional printing machine, and launching the water-ink printing No.1 machine.
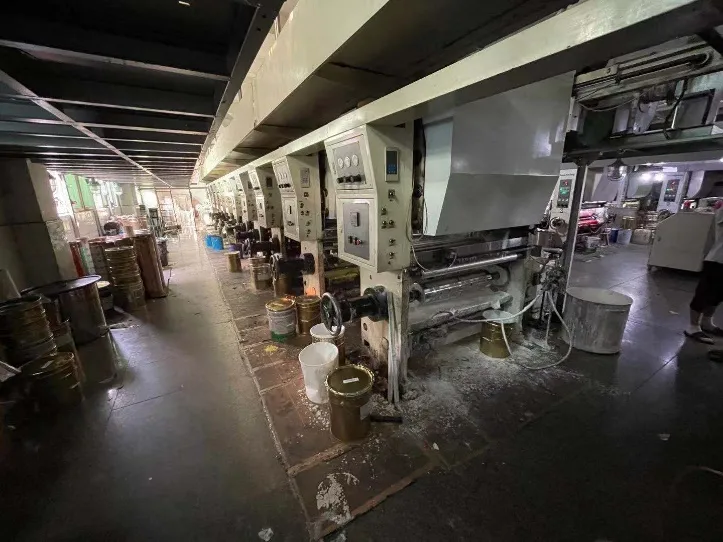
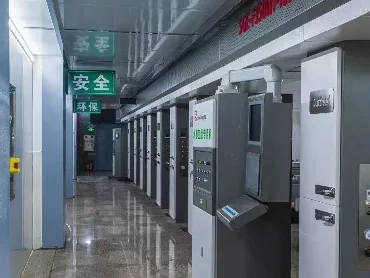
At the same time, the factory workshop was remodeled to create a new experimental ink printing workshop.
At the end of the year, we carried out a lot of experimental improvement and pre-production with the mechanical factory, plate making factory and ink factory, and successfully applied the ink printing process in the official production, now the finished products have exceeded 1,500 tons, and the running speed is stable at 200 m/min. so the ink printing machine No.1 was successfully finished. In the process of production, we collected a lot of data, improved and customized the ink printing machine No.2 and No.3, and at the same time, we rebuilt and upgraded the workshop, which will be completed by the end of 2021 and put into production at the beginning of 2022.
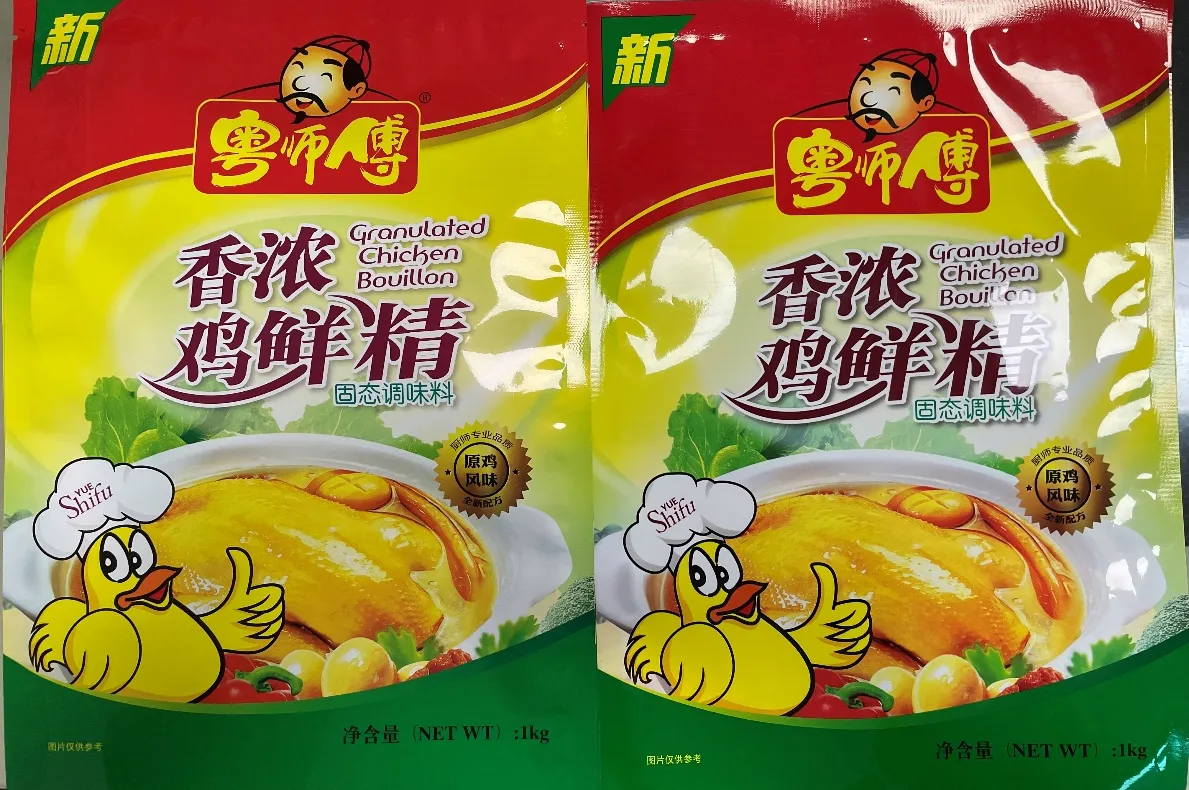
Nowadays, the water-adhesive lamination technology still has some defects, and some product structures cannot be completely replaced. The next plan of our company is to improve the water glue and solvent-free laminating process, and at the same time rebuild the laminating workshop, optimize the conveying chain in the factory, and strive to complete the transformation of the whole production line by the end of 2026, and completely complete the production line “de-solventized”, to realize the green production.
Serving customers with heart, quality as the root, innovation as the basis. This is the production concept of Zhongjia Printing.